Minnesota
Inventors Hall of Fame
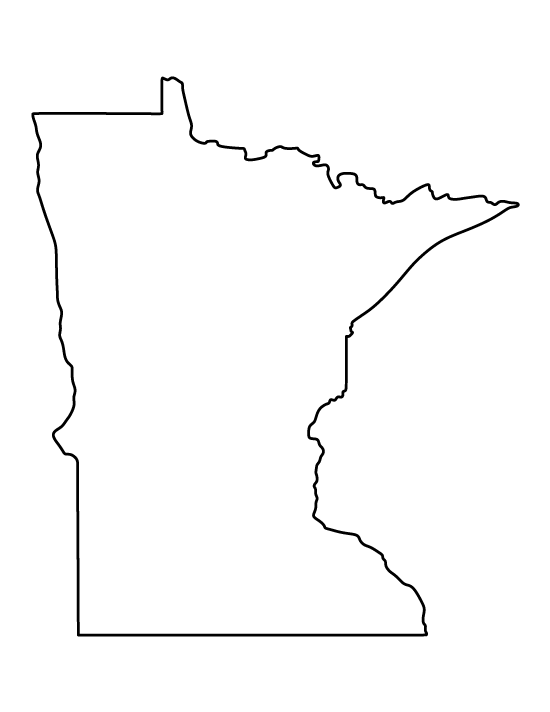
S. SCOTT CRUMP
(1953 - ) S. Scott Crump invented and patented fused deposition modeling (FDM®), a leading technology in the field of additive manufacturing, more commonly known as three-dimensional (3D) printing. The process is used to create functional prototypes and manufactured goods directly from a 3D CAD (computer aided design) program, using high-performance industrial thermoplastics.
One of the essential early steps in the inventing process is creating a prototype to test a new product design. Although engineers and designers have benefitted greatly from computer-aided design, they still need a physical copy to check the viability of their ideas. Making models by hand was a time consuming and expensive process that often started with wood, clay, or foam.
While working as an engineer in the aviation industry, Crump became frustrated with the long lead times needed to make prototypes. He wanted a faster and less expensive process. He was inspired by two-dimensional (2D) plotters, which use an ink pen to create 3D images. If the 2D plotter could be redesigned, then it could be used to make three-dimensional objects.
Crump tested his theories in the family kitchen by making a toy frog for his 2-year-old daughter using a handheld hot glue gun loaded with a mixture of polyethylene and candle wax. He created the toy’s shape layer by layer to simulate the process. Then to automate the process, he modified a 2D plotter to extrude wax and plastic.
He continued experimenting in the kitchen, ruining every good frying pan in the house. When the food started tasting like plastic, his wife convinced him to move the project to the garage, where he devoted many weekends to it.
To accommodate overhanging and hollow regions of the 3D part, he developed a sacrificial support material that can be removed from the completed part. These soluble support materials made it possible to produce complex geometries and cavities difficult to build with traditional manufacturing methods.
His approach worked, but software had to be developed to drive the machine. He spent $10,000 on digital-plotting equipment. Along the way, his wife, Lisa Crump, insisted that he either turn his obsession into a business or give it up. "We had to make a decision as we were spending a lot of money on a hobby," Crump said. In 1998, he and his wife founded Stratasys, Inc.
With the introduction of rapid prototyping machines, such as those made by Crump, a prototype could be made in a matter of hours. The first Stratasys 3-D kit cost $130,000, but had no buyers. Scott decided to develop larger machines, suited for major companies, such as General Motors and 3M, which could afford to buy the expensive product. The larger machine was about the size of a refrigerator. After seven prototypes, a reliable unit was produced and shipped in 1991.
In 1992 Stratasys shipped four units. Crump’s belief in his vision gave him the confidence to press on, even though he had only shipped five systems in his first three years. Stratasys has grown exponentially since then.
Crump has led innovative efforts expanding the 3D printing market from prototyping into virtually every aspect of development and manufacturing. He managed the early work on an innovation used by FDM® machines, the ABS filament, which allowed engineers to formulate fully functional prototypes that have up to 75% of the strength of an actual molded part. This thermoplastic filament is heated to its melting point and then extruded out of a nozzle layer by layer. The extruded material hardens immediately on cooling to form the three-dimensional object.
FDM® printers use two kinds of materials, a modeling material, which constitutes the finished object, and a support material, which acts as a scaffolding to support the object as it's being printed. Crump’s other innovations include the Breakaway Support System (BASS), the Works Soluble Support System, a baffled oven for high temperature build environments, and the Dimension - the first bench-top 3D printer.
There are several different methods of 3D printing, but over the past two decades FDM® has become the most widely used additive manufacturing method for 3-D printing in the world. The fused-deposition modeling process Crump invented has become the core technology behind consumer desktop 3-D printers.
Crump has a mechanical engineering degree from Washington State University and a master's degree in entrepreneurial studies from UCLA. He has 14 U.S. patents, with additional applications pending and many equivalent foreign patents. He is recognized as one of the fathers of 3-D printing technology.
Crump served as Chief Executive Officer, President and Treasurer of Stratasys from 1988 to 2012. In 2012, Crump became the chairman of Stratasys Ltd., a new corporate entity formed by the merger of Stratasys Inc. and Objet Ltd.
Stratasys is a leading manufacturer of 3D printers and production systems for rapid prototyping and manufacturing applications. It has grown into an industry-defining company that has put additive manufacturing into operation with more than 20,000 manufacturers around the world. Additive manufacturing differs from the more traditional 3D sculpting technique, which relies on the removing material (subtractive manufacturing) to form a three-dimensional object.
Stratasys has dual headquarters in Eden Prairie, Minnesota and Rehovot, Israel, and has approximately 1,100 full time employees. Its products are used in the aerospace, defense, automotive, medical, business and industrial equipment, education, architecture, and consumer-product industries.
